Washers have traditionally been used to protect the joint surface from damage during the tightening process and to distribute the load under the bolt head and nut. The stress under the face of a standard hexagon headed nut can result in indentation into standard strength steel surfaces. In recent years washers have started to be replaced by flanged headed fasteners for several reasons that will be discussed in this article. Prior to going into the details, lets look at some background.
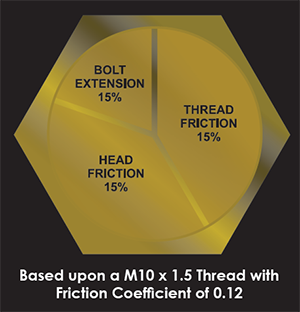
Using torque to indirectly control a bolt’s tension is by far the most popular controlled tightening method. This is due to its simplicity and its widespread understanding by the majority of engineers.
The nominal torque necessary to tighten the bolt to a given tension can be determined either from tables, or, by calculation using a relationship between torque and the resulting bolt tension, or by testing. Friction that acts in the threads of the bolt and under the bolt head dissipates the majority of the tightening torque. For a free spinning nut, only about 15% of the torque is actually used to extend the bolt. The majority of the torque is used to overcome friction under the nut face and in the threads.
The way in which this can affect replacement fasteners is that the original equipment manufacturers (OEMs) specify the tightening torque based upon tests or calculations on the fasteners that are installed on the equipment.
Many OEMs specify flanged headed fasteners for a number of reasons. Using a replacement fastener not of the same type, strength and finish as that originally specified will lead to potentially serious problems since the torque-tension characteristics will be affected. That is, the preload generated by the tightening torque may be insufficient to prevent the joint or the bolt failing.
Flanged headed nuts and bolts have been developed to eliminate the deficiencies that have been found with the use of washers.
Standard washers are typically softer than the nuts and bolts that they are used with and can often plastically deform under the high compressive stress that they must sustain. For higher strength fasteners, this can lead to the washer dishing and indenting resulting in the clamp force being reduced significantly. An example of such a washer is shown in figure 3. Flange headed nuts and bolts do not suffer from this effect since the washer face is as strong as the bolt/nut itself.
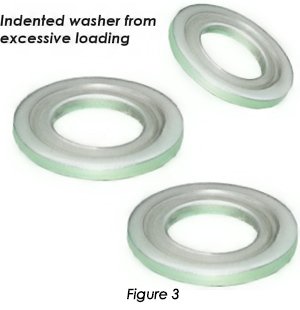
It is not unusual for short grip length joints, with several interfaces, to experience a bolt tension reduction of up to 50%. A joint that may perform satisfactorily when flanged nuts and bolts are used may suffer problems when washers are inserted into the joint. Such a change can invalidate all the calculations and testing pertaining to the joint completed by the manufacturer.
Using a plain hexagon headed nut and bolt without washers will increase the surface pressure under the bolt head and nut face well beyond that which a standard structural steel surface can adequately support. The consequence of this is that the amount of embedding loss is significantly increased resulting in a higher than anticipated bolt tension loss. Essentially the risk is that for short grip length joints, the bolts can come loose without nut rotation occurring. The adverse effect that this can have on the joint’s structural integrity is obvious.
As has been explained, there are several reasons as to why flanged nuts and bolts are preferred over standard hexagon fasteners used with washers. The sensible approach is to replace like fasteners with like fasteners; unless you are feeling lucky.
To overcome the indentation problem, special hardened washers can be used however such washers are not available usually off the shelf. Research conducted in the 1980’s in the U.K. showed that because of the clearance hole in the washer, an eccentric loading can occur that can lead to very high localised stresses. A reasonably large clearance hole in the washer is needed to ensure that the radius that is present under the bolt head does not contact the hole edge. Such clearance on the nut can lead to the washer being tightened eccentrically to the bolt axis. This leads to a high localised load concentration increasing the risk of indentation and joint damage. This effect is illustrated in figure 4.
One further effect that was noted in the UK research was movement of the bearing face during tightening. Normally when the nut is tightened, the nut moves on a stationary washer. However it has been found that sometimes as the nut is being tightened; the washer begins to rotate on the joint surface. That is, the nut and the washer rotate as one. The effect of this is shown in figure 5. The relationship between the applied torque and bolt tension can change. For a given applied torque this can result in a significant loss of bolt tension. Unless careful observation is made during tightening, you will not be able to tell whether this effect has happened or not.
One final consequence of using washers an effect referred to as embedding. Surfaces that may feel flat are anything but flat when viewed under a microscope. A photo of the surface of a zinc plated washer is shown in figure 6 on page 4
As you may be able to predict, when this surface is placed into contact with another, only the tops of the surfaces touch.
Embedding is a result of local plastic deformations that occur under the nut face, in the joint faces and in the threads as a result of plastic flattening of the surface roughness. To some extent, this always will occur when two surfaces are placed in contact and loaded. It is known that the majority of embedding losses arise when the working load is first applied to a joint changing the contact pressures. The amount of loss, essentially the joint becoming ever so slightly thinner under the bolt head and nut face, is typically in the region of between 0.002 to 0.006 mm for each metal to metal steel surfaces. It can be significantly more on surfaces that are painted.
The effect of using washers instead of flanged nuts and bolts is to increase the number of interfaces within the joint. Since each face will sustain an embedding loss, the net effect of using washers is to increase the loss of bolt tension due to this effect. On joints that use bolts that have a relatively short grip length, typical of chassis joints, the additional embedding effect can be particularly pronounced.
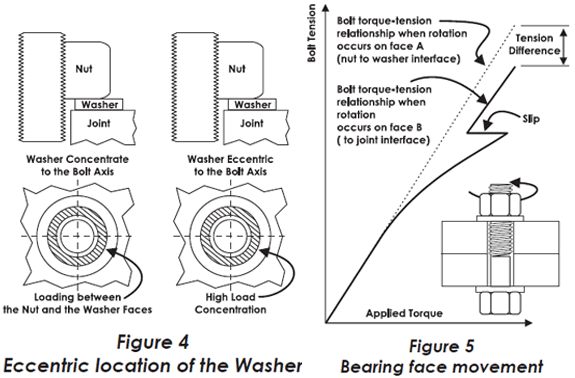
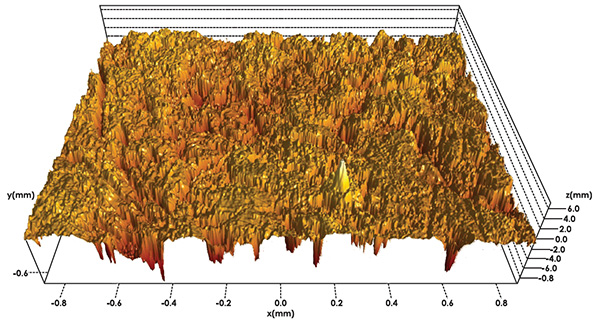
More Bolting information can be accessed from the Bolt Science Website at www.boltscience.com Or alternatively Contact 12PBC on the following numbers:
Phone - +612 8788 8000
Fax - +612 9725 1622 Email – info@12-point-bolts.com